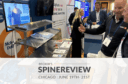
- DinamicOR
-
by feed_admin
The constantly rising costs of delivering quality healthcare, along with shrinking margins, have forced virtually every hospital and ASC in the country to seek ways to cut costs so as to remain profitable. Every phase of process management has come under scrutiny, and hospitals have discovered some surprising information about areas where time and money have been wasted.
Here are three of the biggest areas where waste has led to decreasing profit margins, which means they are prime candidates for any reform initiative.
Decreasing length of stay
Breakdowns in communication between people involved with the release process have always caused significant delays in having patients released promptly. A study that examined this situation found that more than 50 percent of all waste at most hospitals comes from unnecessarily increasing the length of stay for patients. For a 500-bed hospital, this amounts to nearly $2.5 million per year, so addressing this single issue should allow your hospital to realize a huge saving over the course of a year.
Make all rooms energy-efficient
You might be amazed at the achievable savings associated with making all rooms in your hospital truly energy efficient. Bathrooms are an especially profitable area for renovation. You can convert all showers, toilets, and sinks to be low-flow models, and you can have waterless urinals installed to save a ton of money. Of course, this will call for some upfront investment, but once the savings start piling up, you’ll wonder why you didn’t do it sooner.
You can also modify your wiring system so that only necessary lights are routinely used, and all leaky faucets and running toilets should be quickly serviced to prevent waste in those areas.
OR Back Table Organization
When surgical tools and materials in your operating room are stacked on a table, there is typically only 38 percent visibility for all the tools being made available. This results in a great deal of lost time, searching for the appropriate tool for a necessary procedure. Even when the location of the tool is known, it can cause delays in retrieving the tool before usage. Using a back table system that is customizable, replicable, and allows for better organization like the DinamicOR back table solution, can increase OR efficiencies by 33 percent! With DinamicOR, a full 92 percent of all tools and instruments are clearly visible at all times and can instantly be retrieved. This means OR staff are able to achieve the maximum efficiency for organizing all operating equipment, as well as your standard workflow procedures.
These three areas are ones that nearly every hospital and ASC in the country can implement to rack up some major savings. In fact, even in these lean times, they may make your hospital more profitable than it has been for years.